Ekoprodur
S10-HP
Modern and reliable thermal and acoustic
insulation.
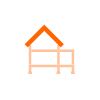
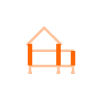
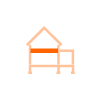
Spray foam insulation systems (PUR) are currently one of the leading products used for thermal insulation. Unprecedented airtightness, superior longevity of parameters and excellent insulation properties are just some of the many advantages of the PCC Prodex foams.
Modern and reliable thermal and acoustic
insulation.
Modern and reliable thermal and acoustic
insulation.
Modern and reliable thermal and acoustic insulation with increased reaction to fire parameters.
A wide range of products used to make foams, either manually or mechanically, for applications in a number of sectors.
These products are designed and specially adapted to the processing machinery and in accordance with individual customer requirements.
I would give our cooperation with PCC Prodex top marks. Their technical support, which I can always count on, is added value in our joint operations on the polyurethane foam market.
Witold Bołądź – Tychy
PCC Prodex has been my supplier of spray systems for 4 years. Our customers’ satisfaction with their insulation is the best proof of the quality of foams produced in Brzeg Dolny.
Dariusz Warzecha – Grudziądz
2023 Copyright © PCC Prodex